WP1 PROJECT MANAGEMENT, DISSEMINATION AND EXPLOITATION
Work Package 1 (WP1) deals with organisational and managerial tasks.
More specially, its objectives are :
- To monitor the technical progress, financial, administrative and legal aspects and plan of the project.
- To consolidate the project planning, progress reports, milestone reports, cost statements and budgetary overviews.
- To facilitate communication with Topic Manager and Clean Sky JU.
- To perform the required activities concerning the dissemination and exploitation of the results.
WP2 SPECIFICATION OF THE ACTUATORS
Work Package 2 (WP2) is dedicated to increasing the physical knowledge of such complex flow control configurations, involving pulsating jets interacting with a boundary layer and then with a rotating wheel.
Moreover, WP2 is also devoted to providing fluidic and geometric parameters to improve the design process of the high-end actuators. To do so, a dual approach with experimental and numerical studies will be used. Experiments will rely on the CME2 test bench (see Figure 6), a single stage, low speed, axial compressor, located at Arts et Métiers Institute of Technology (Lille).
Numerical simulations will be performed using the elsA code from ONERA and advanced methods (hybrid RANS/LES and Chimera technique with overset grids).
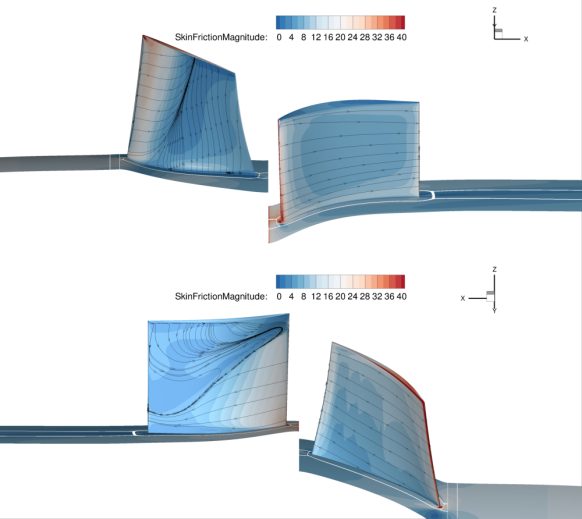
T2.1 Study of the flow physics
The goal of this task is to improve the understanding of the flow mechanisms involved in the transition from normal to stall regimes as well as the ones related to the flow dynamics of the controlled flow by means of CFD (Figure 1) and experiments in a single stage axial flow compressor.
In parallel, the CFD activities at ONERA aim to improve the methodology for the prediction of the controlled flow, with both the Chimera technique (overset grids) and hybrid meshes on one hand, and with hybrid RANS / LES methods on the other hand.
T2.2 Aerodynamic specifications of the actuators for real engine application
The fluidic parameters (location and number of jet actuators, jet width and thickness, momentum, blowing flow angle, frequency, duty cycle) for an optimal control in this configuration will be derived.
T2.3 Numerical simulation of the complete component of the real engine with / without control
A numerical test program will be conducted to check the effectiveness of the sizing of the jets obtained in T2.2.
WP3 DESIGN, TEST AND REALISATIONS OF THE ACTUATORS
The actuators’ design and test are realised in the framework of Work Package 3 (WP3), thanks to the experience and knowledge acquired by one of the project partner (CTEC) during previous projects in aerospace domain, using various kinds of devices relying on amplified piezo - actuators. Several design phases are planned, interleaved with validation of their fluidic performance on a specialised test bench operating at ONERA Lille. Also a validation of their resistance will be performed, taking into account the harsh environmental conditions due to strong thermal and vibratory constraints like those encountered in aircraft engines.
T3.1 Design and manufacturing of a prototype amplified Piezo-electric actuator
- Definition of solutions for electronic amplifiers and for position sensors.
- Definition of electronic open loop control (pre shapers).
- Design of the diffuser geometry, in collaboration with ONERA as regard machining issues and costs.
- Manufacturing of one actuator and electronic.
- Actuator electromechanical tests versus frequency (high level bandwidth).
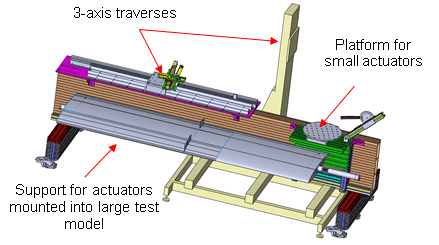
T3.2 Test of the performances of the prototype actuator
Fluidic performances of the AFC prototype (Dedicated test bench existing at ONERA)
Operational Performance :
- Actuator electromechanical tests versus temperatures.
- Vibration tests.
- Thermal calibration and update of open loop control (pre shapers).
T3.3 Design and manufacturing of the optimized actuators
WP4 INTEGRATION AND VALIDATION OF THE AFC SYSTEM IN AERONAUTICS ENVIRONMENT
T4.1 Integration design
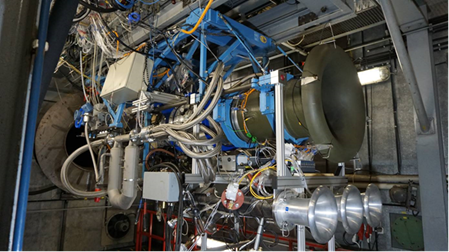
Design of a new casing to be installed in front of the LPC of the Larzac 04 engine.
T4.2 Manufacturing & system integration
New Casing Manufacturing by an external subcontractor Functionality and reliability checks of the actuation system and thorough tests of the installed instrumentation on the shop floor. Performance tests of the clean engine will be performed as a baseline test. Test of the actuation system while the engine is not running and then progressive speed increase of the engine.
T4.3 Engine test and evaluation of results
A synthesis of the results obtained of the experience acquired will be used to propose a roadmap to produce and test higher TRL actuators.