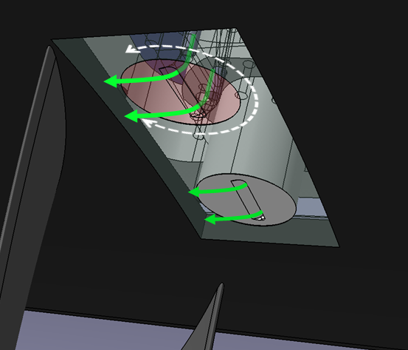
Surge and rotating stall are unstable flow phenomena which can occur in aeronautical compressors operating at low flow rate. They represent serious concerns for flight safety as their arising can lead to some dramatic accidents. Consequently, the engine manufacturers and users introduce safety margin to avoid that surge and rotating stall set-in the compression stages of the engines. They consequently deprive the machine from its higher pressure ratios and higher efficiencies. An improvement of the so-called ‘surge margin’ can directly allow to have a beneficial impact on the engine weight by reducing the number of the compressor stages and thus on its Specific Fuel Consumption.
The present European financed project focus on the extension of the stable operating range of axial compressors by controlling the flow at compressor blade tip thanks to fluidic jets blowing at the machine casing. (Figure 1) The final goals consist of reducing the surge margin by postponing the stall onset. More specifically, the objective of the ACONIT project is to design, manufacture, and test actuators for flow control to integrate in an aircraft engine. The actuators must, therefore, fulfill aeronautics requirement in order to increase the Technology Readiness Level (TRL) in this domain.
To do so, the first objective of the work is to improve the knowledge of the flow physics of an efficient flow control system by joint numerical and experimental analyses performed in a low speed, single stage axial compressor. The results of these analyses will be used to derive the fluidic specifications for a high TRL actuator and control system.
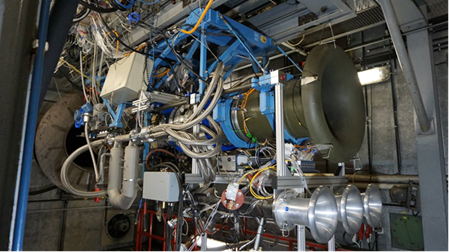
These specifications will be the basis for the design and manufacturing of amplified piezo-electric actuator prototypes whose fluidic and operational performance will be precisely evaluated before manufacturing final actuators to be integrated in a full scale jet engine test vehicle (Figure 2). The performance evaluation will be carried out in an environment with vibrations and controlled level of temperature.
With extensive engine tests, the actuator performance will be evaluated in terms of Surge Margin Improvement, as well as in terms of energy balance between the induced consumption and the engine performance improvements. Our project consortium gathers a SME (CEDRAT TECHNOLOGIES), two academic institutions (Bundeswehr University Munich and Arts et Metiers Institute of Technology) and a Research Center (ONERA). It therefore includes skills ranging from internal flow analysis in turbomachineries, to flow control and actuators design, manufacturing and characterizations by testing supported by CFD. The project duration is from March 2020 to September 2023.